Specifications
1. General
1.1 Scope of work
The work required under this section shall consist of furnishing the
following items of custom hollow metal work as shown on architectural
drawings and as specified herein:
All hollow metal doors
All hollow metal frames
Special hollow metal (as indicated on plans)
Stainless steel as required
Hollow metal panels
Pass through windows
Louver frames
1.2 Work not included:
The following work is specified elsewhere and is not included in this
section:
Installation
Hardware and its installation
Glass and glazing
Structural steel forming, or reinforcement
Field painting
Protection at the building site of items furnished under this section
Field assembly of spliced frames
1.3 Shop drawings
Six (6) copies of all necessary shop drawings shall be submitted to the
Architect for his/her approval. These drawings shall fully describe and locate
all items being furnished. Approved shop drawings shall constitute final
contract requirements, and no work shall be fabricated until the Architect has
approved shop drawings for that work.
2. Products
2.1 Clearances
Edge clearance:
Between door and frame at the head and jamb- 1/8”.
At door sills with no threshold- 5/8” to 3/4” above finished floor or to
suit threshold.
Between meeting edges of door- 1/8”.
(Finished floor is defined as the top surface of the floor and should
correlate with the bottom of the frame.)
2.2 Hollow Metal Doors
A. MATERIALS:
Doors shall be made of commercial quality, level, cold rolled
steel conforming to ASTM designation A-366 and free of
scale, pitting or other surface defects. Face sheets for interior
shall not be less than 16 gauge. Face sheets for exterior doors
shall be not less than 16 gauge and shall be galvanized.
B. Design and Construction:
1. All doors shall be custom made of the types and sizes shown on
approved shop drawings and shall be fully welded seamless
construction with no visible seams or joints on their faces or
vertical edges. Minimum door thickness shall be 1- 3/4”.
2. All doors shall be strong, rigid, and neat in appearance, free of
warpage or buckle. Corner bends shall be true and straight and of
minimum radius for the edge of metal used.
3. Face sheets shall be stiffened by continuous vertical formed
steel hat section spanning the full thickness of the interior
space between door faces. These stiffeners shall be no less
than 22 gauge, spaced not more than 6” apart and securely
attached to the face sheets by spot welds not more than 4”
on center. Spaces between stiffeners shall be sound deadened
and insulated the full height of the door with an inorganic
noncombustible batt-type material.
4. Door faces shall be joined at their vertical edges by a continuous
weld extending the full height of the door. All such welds shall
be ground, filled, and dressed smooth to make them invisible
and provide a smooth, flush surface.
5. Top and bottom edges of all doors shall be closed with a
continuous recessed steel channel not less than 16 gauge,
extending the full width of the door and spot welded to both
faces. Exterior doors shall have an additional flush closing
channel at their top edges and, where required for attachment
of weather-stripping, a flush closer of exterior doors to permit
the escape of entrapped moisture.
6. Edge profiles shall be provided on both vertical edges of doors
as follows:
a. Single-acting swing doors – beveled 1/8” in 2”
b. Double-acting swing doors – rounded on 2-1/8” radius
7. All hardware furnished by the hardware contractor for single-
acting doors shall be designed for beveled edges as specified in
subparagraph 6 above.
8. Hardware reinforcements:
a. Doors shall be mortised, reinforced, drilled, and tapped at the factory
for fully templated hardware only, in accord with the approved
hardware schedule and templates provided by the hardware
contractor. Where surface mounted hardware is to be applied, doors
shall have reinforced plate only; others shall do any drilling and
tapping, which includes through bolts.
b. Minimum gauges for hardware-reinforcing plates shall be as follows:
Hinge and pivot reinforcement: 7 ga.
Reinforcements for lock face, flush bolts, concealed holders,
concealed or surface mounted closers: 12 ga.
Hardware: 12 ga.
9. Glass mouldings and stops (if applicable):
a. Where specified or scheduled, doors shall be provided with hollow
metal mouldings to secure glazing by others in accordance with glass
opening sizes shown on approved shop drawings.
b. Fixed mouldings shall be securely welded to the door on the security side.
c. Loose stops shall not be less than 16-gauge steel. With butt corner
joints, secure the frame opening by cadmium or zinc-coated
countersunk screws.
10. (If applicable) Louvers shall be of the welded blade type of
construction (providing the free air area specified by the
Architect). Louvers pierced into the face sheets will not be
permitted.
Finish: After fabrication, all tool marks and surface imperfections shall
be dressed, filled, and sanded as required to make all faces and vertical
edges smooth, level, and free of all irregularities. Doors shall then be
chemically treated to ensure maximum paint adhesion and shall be
coated, on all exposed surfaces, with a rust-inhibitive primer, which is
fully cured before shipment.
2.3 Panels
Hollow metal panels shall be made of the same materials and constructed
and finished in the same way specified for hollow metal doors.
2.4 Gauges
A. Exterior doors 16 gauge
B. Interior doors 16 gauge
2.5 Hollow metal frames
A. MATERIALS:
1. Frames for exterior openings shall be made of commercial grade cold-
rolled steel conforming to ASTM Designation A366-68, not less than
16 gauge, and shall have a zinc coating.
2. Frames for interior openings shall be either commercial grade cold
rolled steel conforming to ASTM A366-68 or commercial grade hot
rolled and picked steel conforming to ASTM A569-66T. Metal
thickness shall be not less than 16 gauge for frames in openings 4’0”
or less than 16 gauge for frames in openings 4’0” or less width.
B. DESIGN AND CONSTRUCTION:
1. All frames shall be custom made welded units with integral trim, of
the sizes and shapes shown on approved shopped drawings. Knocked
down frames will not be accepted.
2. All finished work shall be strong and ridged, neat in appearance,
square, true and free of defects, warps or buckle. Moulded members
shall be clean cut, straight and of uniform profile throughout their
length.
3. Jamb depths, trim, profile, and backbends shall be as scheduled by
the Architect and shown on approved shop drawings.
4. Corner joints shall have all contact edges closed tight, with trim faces
mitered and continuously welded, and stops butted. The use of
gussets will not be permitted.
5. Minimum depth of stops shall be 5/8”. Cutoff (sanitary or hospital
type) stops, where scheduled, shall be capped (at 45 degrees or 90
degrees) at heights shown on approved shop drawing.
6. When shipping limitations so dictate, frames for large openings shall
be fabricated in sections designed for splicing in the field by others.
7. Frames for multiple or special openings shall have mullion and /or
rail members which are closed tubular shapes having no visible seams
or joints. All joints between faces of abutting members shall be
securely welded and finished smooth.
8. Hardware reinforcements:
A. Frames shall be mortised, reinforced, drilled and taped at the
factory for full templates mortised hardware only, in accord
with approved hardware schedule and templates provided by
the hardware contractor.
Where surface-mounted hardware is to be applied, frames shall
have reinforced plates only; and drilling and tapping shall be
done by others.
B. Minimum thickness of hardware reinforcing plates shall be as follows:
1. Floor Anchors:
Floor anchors shall be securely welded inside each jamb
with two holes provided at each jamb for floor anchorage.
2. Jamb Anchors:
a. Frames for installation in masonry walls shall be
provided with adjustable jamb anchors of the (t-strap
or stirrup-and-strap) type. Anchors shall be not less
than 2”x10” in size, corrugated and/or perforated. The
number of anchors provided on each jamb shall be as follows:
-Frames up to 7’6” – 3 anchors
-Frames 7’6” to 8’0” – 4 anchors
-Frames over 8’0” – 1 anchor for each 2’ or fraction thereof in height
b. Frames for installation in stud partition shall be provided
with steel anchors of suitable design, not less than 16
gauge thickness, securely welded inside each jamb as follows:
-Frames up to 7’6” – 3 anchors
-Frames 7’6” to 8’0” – 4 anchors
-Frames over 8’0” – 5 anchor plus one additional for
each 2’ or fraction thereof over 8’0”
c. Frames to be anchored in previously placed concrete,
masonry or structural steel shall be provided with
anchors of suitable design as shown on approved shop
drawings. Others shall provide fasteners for such anchors.
i. Dust cover boxes (or mortar guards) of not thinner
than 26-gauge steel shall be provided at all
hardware mortises.
ii. All frames shall be provided with a steel spreader
temporarily attached to the feet of both jambs to
serve as a brace during shipping and handling.
iii. (If applicable) Loose glazing stops shall be of
cold-rolled steel: not less than 18-gauge
thickness, butted at corner joints and secured
to the frame with countersunk cadmium or zinc
plated screws. Loose stops at exterior frames
shall be placed on the exterior side of the frames.
3. Finish:
After fabrication, all tools marks and surface imperfections
shall be removed, and exposed faces of all welded
joints shall be dressed smooth. Frames shall then be chemically treated to
ensure maximum paint adhesion and shall be coated on all inhibitive primer,
which is fully cured before shipment.
4. Labeled doors and frames:
a. Labeled doors and frames shall be provided for those
openings requiring fire protection ratings as determined
and scheduled by the Architect. Such doors and frames
shall be constructed as tested and approved by
Underwriters Laboratories or other nationally recognized
testing agency having a factory inspections service.
b. If any door or frame specified by the Architect to be fire
rated cannot qualify for appropriate labeling because of its
design, hardware or any other reason, the Architect shall be
so advised before fabricating work on that item is started.
3. EXECUTION
3.1 Site Storage and Protection of Materials
A. It shall be the responsibility of the general contractor to see that any
scratches or disfigurements caused by shipping or handling are promptly
cleaned and touched up with a rust inhibitive primer, and that materials
are properly stored on planks or dunnage, in a dry location, and covered to
protect them from damage.
B. Doors shall have their wrappings or coverings removed upon delivery at
the building site and shall be stored in a vertical position, spaced by a
blocking to permit air circulation between them.
NOTE TO ARCHITECT: In that section of specifications where installation of the work
is specified, it should be required that:
- Prior to installation, all frames must be checked and corrected for rack
twist and out of square. Frames must reset true and plumb and remain in
alignment until permanently built into the wall. - Proper door clearances must be maintained in accordance with part 2, section
2.2 of the specifications for custom hollow metal doors and frames, except for
special conditions otherwise noted. Where necessary, metal hinge shims are
acceptable to maintain clearances. Hardware must be applied in accordance
with hardware manufacturer templates and instructions.
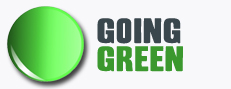
